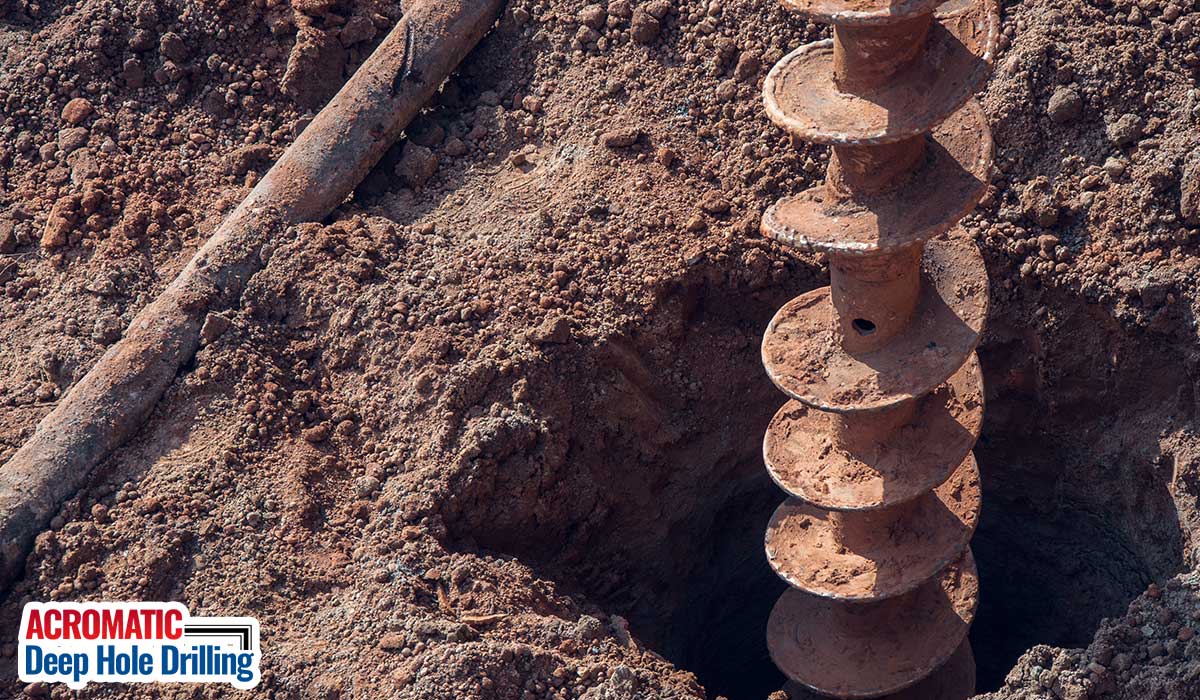
The automotive industry is always looking for ways to make vehicles more efficient with lower cost, more power and performance output and higher efficiency. To do that, engineering is a key element in creativity. That has led to multiple design breakthroughs and integrations of parts for delivery of different needs to make a vehicle work. Automotive drilling has been one of those aspects that allow parts to be both assemblies as well as delivery systems in the same design. This cuts down on multiple hoses and conduits and instead provides a singular part that performs multiple benefits.
How Do You Drill an Automotive Deep Hole?
The first step in any kind of deep hole drilling that impacts the performance of a machine, especially a car engine or similar, involves clean, accurate engineering and design. Once the specs are known, then it becomes a matter of producing a consistent drilling cavity each time to match the expectations calculated as optimum for the purpose. Repeatability is key; a vehicle manufacturer needs to know it can depend on a supplier to deliver the given number of parts ordered, each meeting criteria as ordered.
Once the instructions are confirmed, then comes the application. The practical application of a drilled cavity is to use a drill, of course. However, extended length cavities require more than just a simple drill head. Instead, the drilling has to be progressive and penetrating while still maintaining stability for the direction, length and width expected. This only happens with mechanically insisted drilling tool equipment. While in earlier days, expert artisans applied the work; today, computer-aided or computer-controlled tooling handles the challenge.
Which Drills are Used for Deep Hole Drilling?
The typical deep hold drilling equipment involves a mechanical drilling system that then has extended rods. This can be either one apparatus or it can have the ability to add extensions. There is also a lubrication delivery system. Usually, the drill itself is hollow, which then allows for the lubrication to flow into the drill cavity and drill point, keeping the drill head cool and flowing the debris out of the cavity as it is being worked on. The length of the work and size often dictates the type of deep hole drilling applied, with stronger systems used for larger and deeper work. This is common in automotive orders utilizing drilling on metal parts.
How Does Deep Hole Drilling Work?
The activity depends on the power used to generate the drill, a good drill head that does the hard work effectively, and accurate accessories that can handle adjustments for different job needs. The hard part is not the creation of the drill cavity but controlling it as the hole goes deeper and deeper. A big problem is maintaining the power to keep working at extended lengths while still remaining accurate and avoiding wobble or variation. Dubbed “runout control,” deep hole drilling systems incorporate features that maintain stability as well as power, especially when the distance has to jump from a small 5x diameter to now a 30x diameter, for example. Why does this matter? The runout dictates the tool distance or length that needs to be applied. Knowing accurately what this dimension will be saves on tool damage and ensures using the right equipment for the task.
Deep hole drilling doesn’t come without a cost, however. Tools wear down and burn out. And that can cause unexpected damage or worse, waste. The goal is to match the right tool length and power so that it’s not under-powered. Otherwise, things break quickly, driving up tooling costs.
What are the Automotive Deep Hole Drilling Difficulties?
For those unfamiliar with the term “drill walking,” it involves the drill head, under pressure, moving off target. Many times, when drilling manually, an artisan takes a nail or metal bit and hammers a small dent exactly where the drill head should go. This provides a point where the drill head can bite into the target material and stay on target, digging deep before pressure causes it to wobble off. With automated drilling, however, things have to move much faster, so drill walking becomes a real problem, creating waste and fouled parts. Longer drills have a strong tendency to wobble, so things are done to offset this. First, a drill point is kept sharp for a quick bite to begin with. Alternatively, a center drill feature can be used to guide the drill head to the target point. It’s a bigger version of punching a divot discussed above. Pilot drilling or double drilling works as well. A smaller, shallow drill point is made first, and then the longer deep hole drill is applied.
A second common problem involves debris or chip control. As a drill works, it produces waste. That can create grind or friction inside the cavity unless it exits. Many drill systems use lubrication flow to keep the drill cool as it grinds against the material as well as pushing out the debris from the cavity. Older machines are a problem, lacking flow systems or viable lubricant delivery. Most deep hole drilling today is applied with an internal lubrication flow approach. It just makes far more sense.
As a third issue, hole or cavity straightness is the hallmark of high-quality deep hole drilling. With short-length drills, such as six inches, this isn’t much of a problem. However, when talking about twenty or thirty inches of length, keeping a drill head straight and on target is entirely another challenge altogether. Again, rigidity is essential to keep things on track, and this is done either by adding extensions to the drill rod or using a longer drill with bracing and shock absorption.
Good Works Comes with the Right Tooling and Expertise
Acromatic Deep Hole Drilling has been providing deep hole drilling for clients for years, including high-quality automotive work. Experience cuts down tremendously on waste and mistakes, and it helps valuable tooling last longer as well. Because Acromatic Deep Hole Drilling combines both, we are able to handle some of the more complex demands from the automotive industry as well as others. Contact us to find out more and how we can help with your next project scope.